Cost-Saving Measures for Engineering Precision Parts
At Procut-cnc, we understand that precision and quality are paramount, but achieving these doesn’t have to come at an excessive cost. By implementing smart engineering strategies and manufacturing optimizations, we help our clients reduce expenses without compromising the integrity or performance of their components. Here’s how we make it happen:
Cost-Saving Measures for Engineering Precision Parts
At Procut-cnc, we understand that precision and quality are paramount, but achieving these doesn’t have to come at an excessive cost. By implementing smart engineering strategies and manufacturing optimizations, we help our clients reduce expenses without compromising the integrity or performance of their components. Here’s how we make it happen:
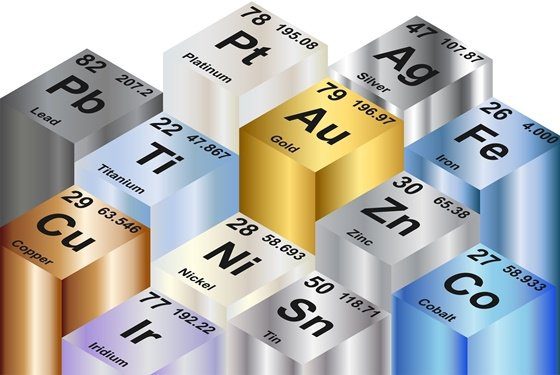
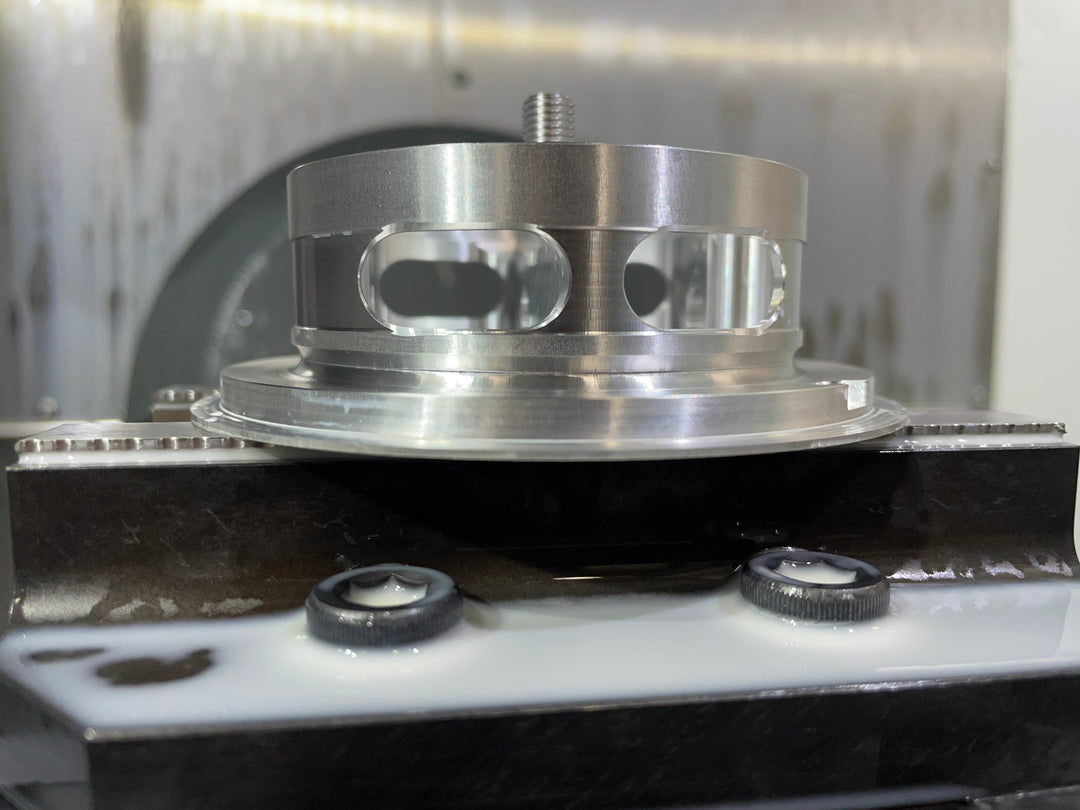
Simplifying Part Design
Complex designs can increase machining time and costs. Our experts collaborate with you to:
- Streamline Designs: Reduce unnecessary complexity in part geometry to lower machining time and tool wear.
- Consolidate Features: Combine multiple components into a single part where possible, reducing assembly costs.
Example: Modifying a design to eliminate hard-to-machine undercuts or deep pockets can cut production costs significantly.
Leveraging Advanced Machining Technologies
Our state-of-the-art equipment allows us to:
- Use 5-Axis Machining: Fewer setups mean reduced labor costs and faster production times for complex geometries.
- Implement Swiss Machining: Ideal for high-volume small parts, this technology increases efficiency and consistency.
- Optimize Toolpaths: Advanced software minimizes cycle times and maximizes tool life.
Result: Reduced machining hours and lower overall project costs.
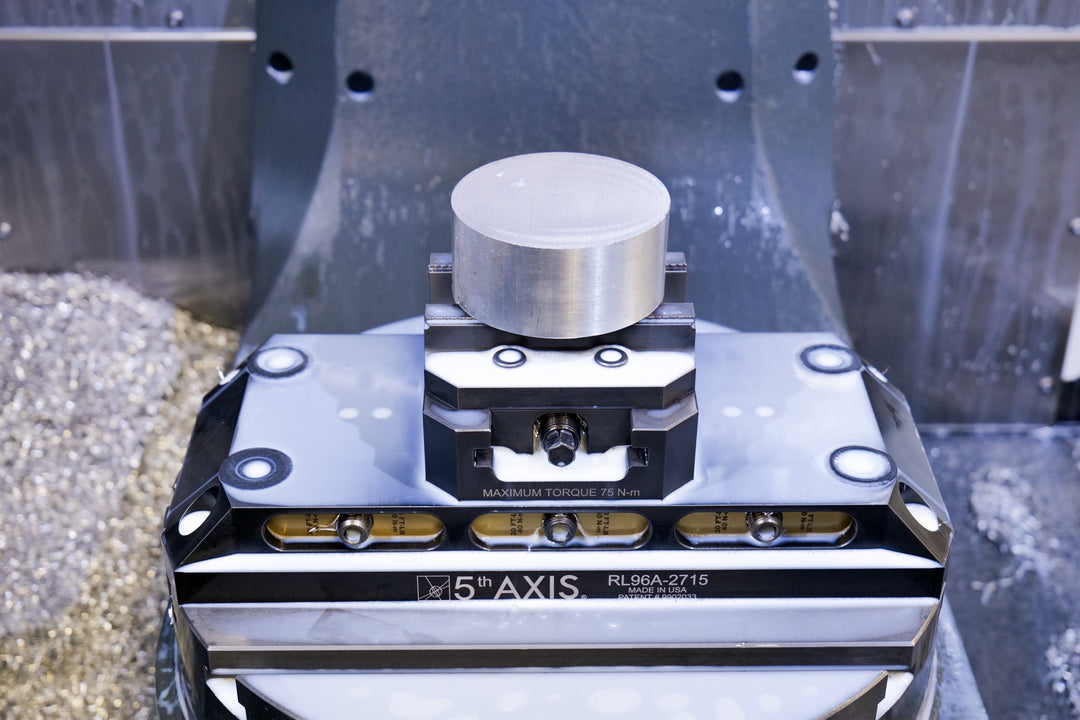
Prototyping Before Full Production
Investing in a prototype ensures that your design is production-ready:
- Identify Potential Issues: Catch and correct design flaws early, avoiding costly adjustments during production.
- Test for Functionality: Verify material and performance requirements before scaling up.
Our Approach: We offer rapid prototyping services to help you refine your design quickly and cost-effectively.
Batch Production and Volume Discounts
Producing parts in bulk offers economies of scale:
- Optimize Setup Costs: Spread setup time and expenses over a larger production run.
- Leverage Bulk Material Purchasing: Lower material costs when ordering in volume.
Procut CNC Advantage: Our production machining capabilities ensure consistent quality across high-volume orders, saving time and money.
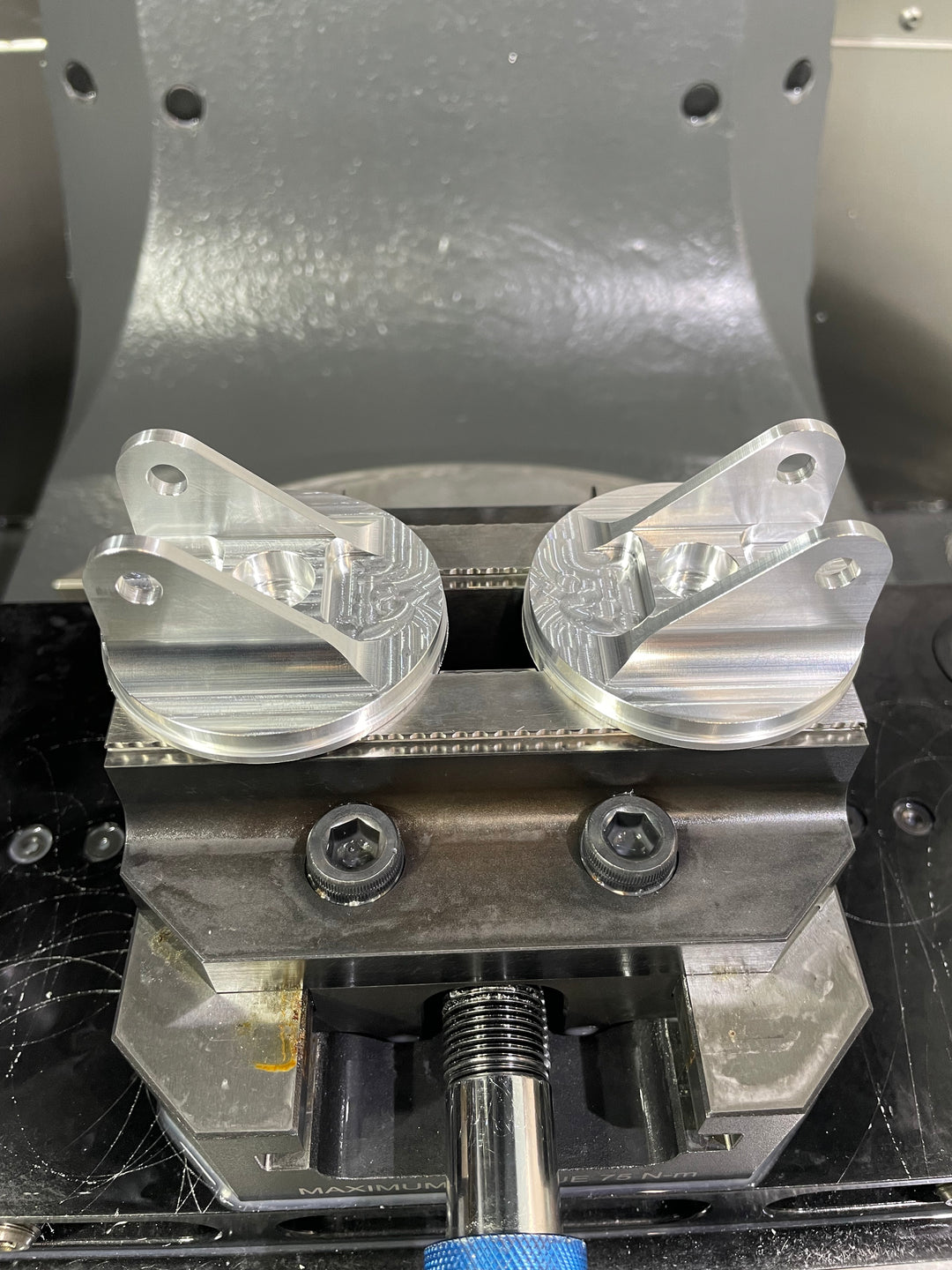
Reducing Tolerances Where Possible
Tight tolerances require extra machining time and increased inspection effort. By working closely with your team, we can:
- Adjust Tolerances: Ensure tolerances are tight only where they are critical to function.
- Focus Precision Where It Matters: Avoid over-engineering non-essential features.
Example: Adjusting tolerances on non-critical dimensions can significantly lower costs without affecting performance.
Utilizing Cost-Efficient Finishing Techniques
Certain finishes may be unnecessary for the part’s intended use. Our team helps identify:
- Functional Finishes Only: Apply coatings or finishes only where necessary, such as anodizing for corrosion resistance.
- Avoiding Over-Specification: Use simpler finishes for non-cosmetic or internal components.
Material Plating
Plating enhances metal surfaces with added durability, corrosion resistance, and aesthetic appeal for various industrial and decorative applications.
Powder Coating
Powder coating offers a durable, eco-friendly finish with superior resistance to wear, corrosion, and fading, perfect for a variety of applications.
Open Communication and Collaborative Engineering
Collaboration is key to cost savings:
- Design for Manufacturability (DFM): Our engineers review your design for efficiency, suggesting modifications to simplify production.
- Transparent Feedback: We work as your partner to find the most economical solutions.
Result: A seamless process that ensures cost-effective production while meeting your performance requirements.
FAQs
A Blanket Purchase Order (PO) is an agreement with a supplier to buy goods or services in bulk over a specified time at a pre-negotiated price. Here’s how it helps save money:
- Volume Discounts: Buying in bulk reduces the per-unit cost of items.
- Price Lock: Protects you from market price fluctuations during the contract period.
- Reduced Administrative Costs: Fewer purchase orders mean less paperwork and processing time, saving on operational costs.
Yes, we gladly accept blanket purchase orders (POs) to help streamline your procurement process.
Procut CNC offers cost-effective contract manufacturing solutions tailored to your needs. Here’s how we help you save:
- Lower Overhead Costs: We handle production, so you don’t need to invest in expensive machinery or facilities.
- Bulk Discounts: Our partnerships with trusted suppliers enable us to secure materials at competitive prices.
- Efficient Production: With our advanced CNC machining capabilities, we ensure precise, high-quality parts, reducing waste and rework expenses.
Procut CNC ensures top-quality and reliable contract manufacturing through a cutting-edge ERP system. This system provides real-time production tracking, automated quality checks, and detailed data analysis to guarantee every part meets exact specifications. It optimizes material usage and machine efficiency, reducing waste and costs.
The ERP also streamlines communication, maintaining clear records and seamless collaboration, while integrating with suppliers to ensure on-time material deliveries and cost-effective production. By leveraging this advanced technology, Procut CNC delivers consistent, high-quality parts with efficiency and reliability.